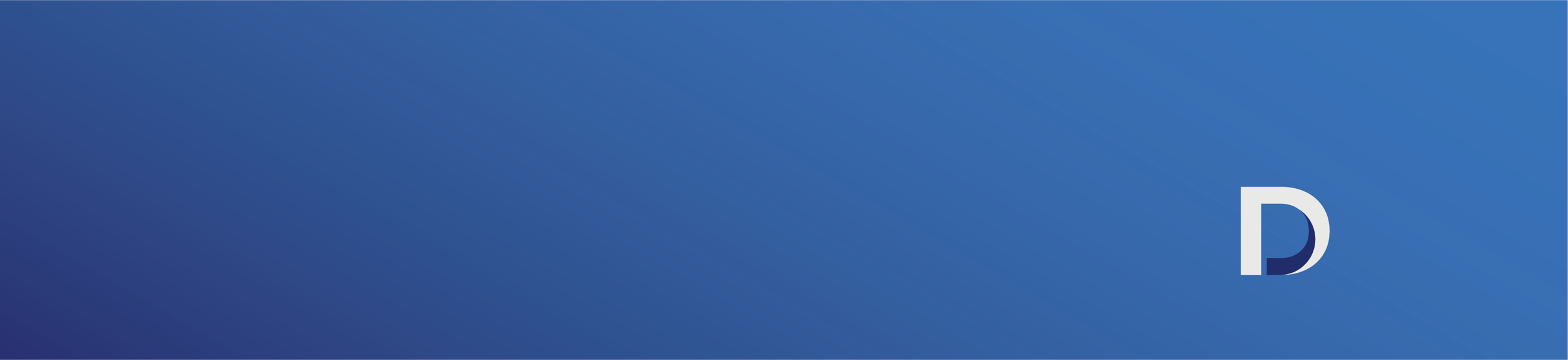
INdustrialization Project for HIGH tech industry equipment
Objective:
To transition a high-tech equipment prototype or concept into a scalable, cost-effective, and production-ready product that meets quality, regulatory, and market requirements.
1. Feasibility Analysis and Planning
Technical Feasibility:
Assess the readiness of the prototype for industrialization.
Identify potential engineering challenges and constraints.
Market Analysis:
Validate demand, customer needs, and competitive positioning.
Define production volumes and scalability targets.
Financial Feasibility:
Estimate production costs, pricing, and ROI.
Evaluate initial investments in tooling, equipment, and resources.
2. Define Industrialization Requirements
Functional Requirements:
Finalize product specifications, features, and performance metrics.
Regulatory and Compliance Requirements:
Identify certifications required (e.g., ISO, CE, FCC).
Ensure compliance with industry standards.
Production Requirements:
Determine production volumes, automation levels, and material sourcing.
3. Design for Manufacturability (DFM) and Assembly (DFA)
Optimize product design to simplify manufacturing and reduce costs.
Minimize the number of components and use standardized parts.
Perform failure mode and effects analysis (FMEA) to mitigate risks in production.
4. Prototype Refinement and Testing
Build pre-production prototypes (alpha and beta versions).
Conduct rigorous testing for performance, durability, and reliability under operational conditions.
Incorporate feedback to refine design and processes.
5. Supply Chain and Vendor Development
Identify and qualify suppliers for critical components and materials.
Negotiate contracts to ensure cost efficiency and supply reliability.
Develop contingency plans for key supply chain risks.
6. Production Process Development
Tooling and Equipment:
Design and procure custom tooling, jigs, and production equipment.
Process Design:
Develop workflows and standard operating procedures (SOPs).
Implement quality assurance (QA) and quality control (QC) processes.
Digital Integration:
Leverage Industry 4.0 tools (e.g., IoT, AI, robotics) for process optimization.
7. Pilot Production Run
Perform a small-scale production run to validate processes.
Monitor output for defects, efficiency, and consistency.
Collect data to refine production methods and address bottlenecks.
8. Full-Scale Production and Launch
Ramp up production to meet market demand.
Monitor performance metrics, including yield rates, production speed, and cost.
Coordinate logistics for distribution and inventory management.
9. Post-Launch Optimization
Collect customer and market feedback to identify improvement areas.
Continuously refine manufacturing processes for cost reduction and efficiency.
Update product design to accommodate evolving technology or standards.
10. Sustainability and Scalability
Introduce sustainable practices (e.g., energy-efficient processes, recyclable materials).
Plan for scaling production to meet future growth and market expansion.